Marcopolo inaugura un nuevo centro de fabricación en Ana Rech
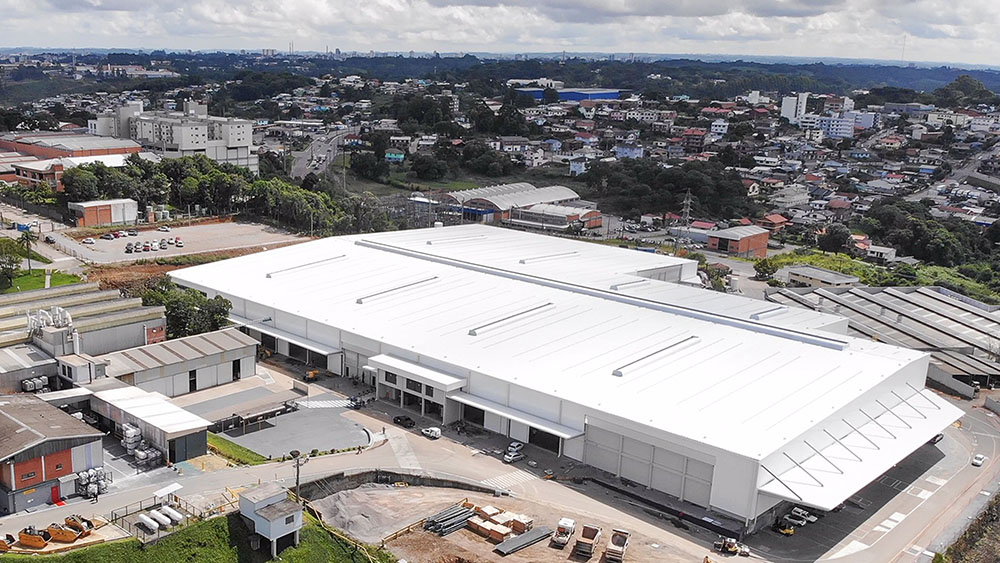
Con una inversión total de R$ 70 millones, la planta es la más moderna y avanzada de la empresa.
El 24 de enero, Marcopolo inició las operaciones de su nuevo Centro de Producción de componentes y subconjuntos metálicos. Con una inversión total de cerca de R$ 70 millones, de los cuales R$ 30 millones ya fueron invertidos, la nueva planta es la más moderna y avanzada de la empresa y tiene como objetivo unificar el ensamblaje de los componentes y subensamblajes metálicos que componen las carrocerías de los autobuses, que fueron ejecutados en diferentes sitios, con la oportunidad de mejorar la productividad y la sinergia.
Con una superficie total de 19.600 m² construidos, el nuevo Centro de Fabricación contará inicialmente con 180 empleados y reunirá las instalaciones, equipos y procesos más avanzados.
El Centro de Fabricación aporta nuevos conceptos de producción que permiten la renovación natural del aire por convección (bienestar térmico para los empleados), cubierta y revestimiento lateral con aislamiento térmico, toda la iluminación LED con atenuación (atenuación automática), proporcionando menor costo y mayor confort visual y seguridad; instalaciones planificadas y organizadas en racks de tuberías y/o canales, proporcionando mayor protección en el flujo de personas y transporte de materiales, mejor condición para el mantenimiento eléctrico, neumático, hidráulico y de gas; infraestructura preparada para recibir equipos con tecnologías de la industria 4.0 (como dos máquinas italianas de última generación que se instalarán en marzo - los empleados fueron a Italia para recibir formación en programación y operación de las nuevas máquinas); toda el área de circulación externa (movimiento de camiones cargados con materia prima) en hormigón, aumentando la vida útil y eliminando prácticamente el mantenimiento del suelo.
Según Júlio Igansi, Gerente de Ingeniería de Procesos, entre los principales diferenciales del nuevo Centro de Fabricación se encuentran la unificación y racionalización de recursos, el flujo continuo de producción y logística, y la gestión visual de todo el proceso productivo.
“La planta es extremadamente segura y cumple con los principios de LEAN, centrándose en la eliminación de residuos, estándares de eficiencia e incluso una mayor calidad para los clientes internos y externos”, dice Julio.
En el nuevo centro se están llevando a cabo las siguientes operaciones: corte por láser de tubos, corte con sierras de tubos automatizadas, corte de tubos robotizado.
Para ello, la unidad cuenta con máquinas automáticas de conformado de tubos, celdas de soldadura robotizadas y celdas de ensamblaje con el concepto de mini-fábricas para el ensamblaje de componentes y subensamblajes. Toda la operación es regulada por el departamento de expedición logística al final del proceso y existe un “supermercado” intermedio para regular y estabilizar la producción, además de preparar los kits de componentes para la célula de montaje.
Las áreas de fabricación que conforman el centro de fabricación son:
- Célula de corte de tubos por láser;
- Célula de conformado de tubo;
- Célula de corte por láser de chapa;
- Célula de corte para punzonadoras de chapa;
- Célula de corte por plasma para planchas;
- Centro de plegado de hojas automatizado;
- Célula de guillotina;
- Célula de prensa con área de utillaje para el mantenimiento preventivo y correctivo, habiendo planificado la realización del preajuste;
- Nueva línea de tratamiento superficial de aluminio y acero;
- Línea de montaje para puertas de aluminio y aberturas laterales;
- Célula de fabricación de varios mecanismos;
- Células de montaje y soldadura.
Según Lusuir Grochot, Director de Operaciones Industriales, el proyecto atiende la producción a partir de la demanda del cliente (producción tirada), con una cadencia definida, menor stock de materias primas y componentes en proceso, menor movimiento de materiales y personas y menor necesidad de transporte. “Todo para ser lo más eficiente, seguro y productivo posible”, comenta Lusuir.
Historia del proyecto del Centro de Fabricación
El proyecto de desarrollo y construcción del Centro de Fabricación comenzó en noviembre de 2017, donde se creó un equipo multidisciplinario para planificar, diseñar y ejecutar el proyecto. En este proceso participaron 223 empleados con sugerencias.
Se creó un modelo, utilizando el método 3P, con un microdiseño de la planta y sus 305 equipos. El 28 de febrero de 2018 se inició la construcción de la nueva planta, que finalizó a finales de diciembre. Once kaizens fueron realizados en 692 horas de los 75 empleados que formaron el equipo dedicado.
La realización de los 11 kaizens tuvo como objetivo aplicar la metodología de los siete defectos al Centro de Fabricación: tiempo de espera; sobreproducción; transporte; procesamiento innecesario; defectos; manipulación e inventario. Crédito das imagens: Gelson Mello da Costa